Stonebridge Estate, London
Innovative Nexus XI soffit support system ensures brickwork perfection for Stonebridge’s impressive new council homes development.
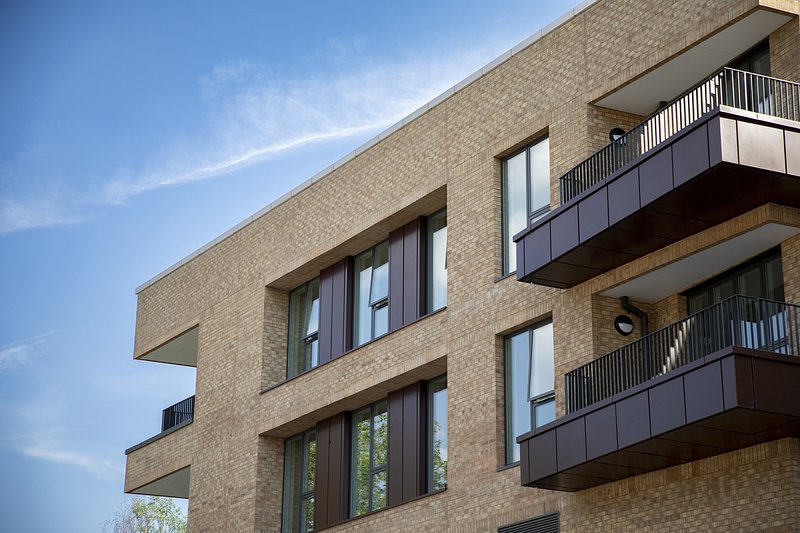
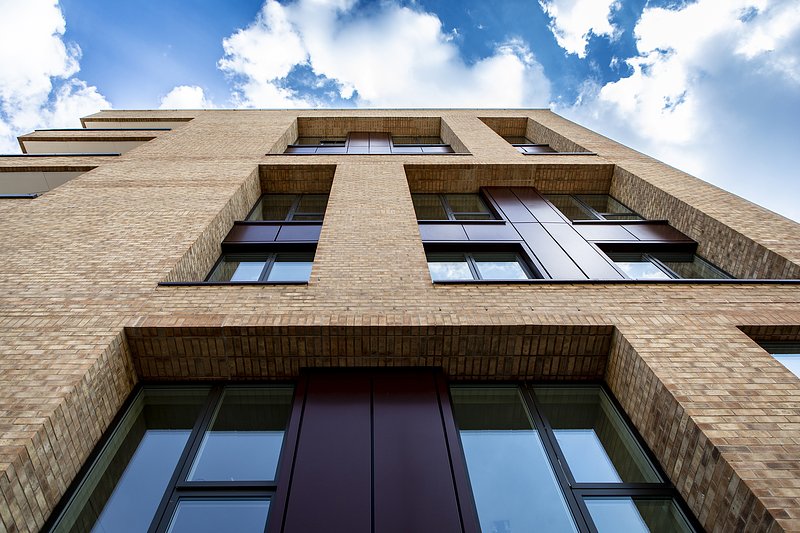
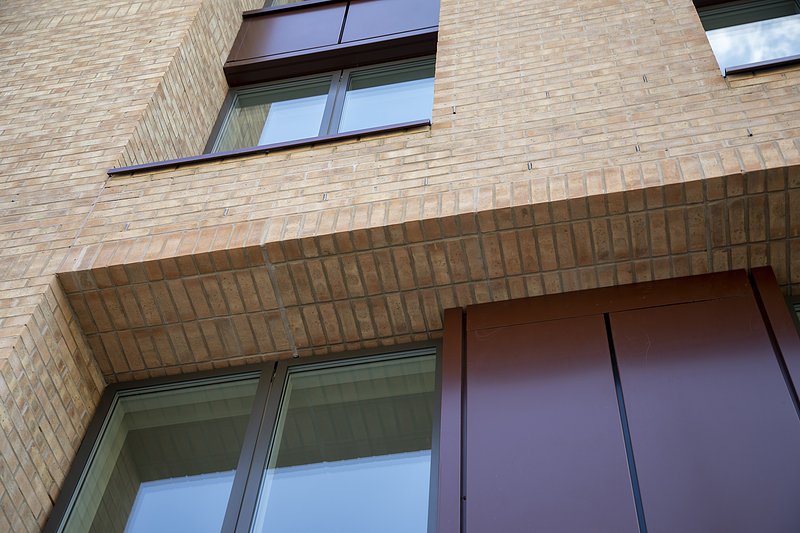
Part of a masterplan by Brent London Borough Council to redevelop the heart of Stonebridge, and provide much needed new homes for residents, the project provides a total of 73 modern, purpose built affordable residential units across two adjacent sites, linked by a new public open space with playground and outdoor gym.
Constructed on a former car park, the development comprises two distinct sections. The larger, Hillside site, is constructed across two blocks, up to 7 storeys in height and linked at first floor level by a landscaped podium and under-croft car park. It comprises a mix of 51 one, two and three-bedroom apartments, each with dual aspect and private balcony. Complementing this, the smaller Milton Avenue site, constructed over three storeys, features a total of 22 4-bedroom townhouses.
Designed and built by community construction specialist, Higgins Partnership, the development echoes the distinctive architectural style adopted for the new Stonebridge community, with a contemporary brick façade, punctured by large, recessed story-height windows and feature open balconies.
The Challenge
The buildings are constructed around a central reinforced concrete frame, with the brickwork façade supported at each storey by Ancon MDC stainless steel bracket angle support, fixed directly to the edge of the cast concrete floor slab. In order to achieve the precision finish required, feature hanging soffits and lintels were required around all larger openings and window heads.
The challenge was to find a solution that would be quick and easy to manoeuvre and fix on site, as well as adjustable to maintain a seamless junction with the supported brickwork above.
Masonry Support Systems and Lintels (PDF, 10 MB)
The Solution
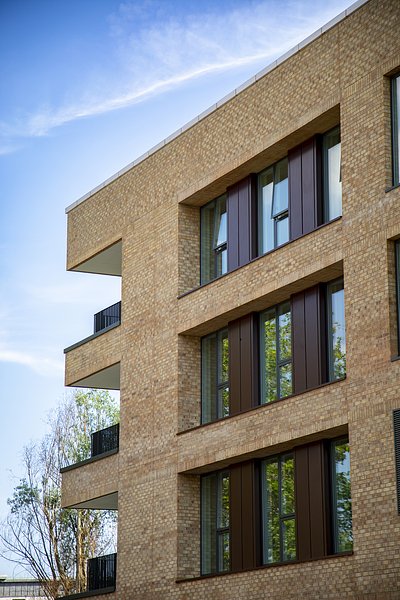
The decision was taken to use the Nexus XI range of brick-faced soffit and lintel systems, developed by Leviat in conjunction with Ibstock Kevington, the UK’s largest manufacturer and supplier of cut-brick systems.
The soffit system, which is manufactured off-site under factory conditions, features a lightweight stainless steel unit faced with precision-cut brick slips, which is simply bolted to the underside of the pre-fixed Ancon MDC support angle. A unique and innovative three-point mechanical fixing system holds the brick slips permanently in position and gives the unit a Class A1 fire rating for use above 18m, enabling it to be used throughout the project.
At less than half of the weight of a traditional cast system, the Nexus XI units could be simply lifted and hand-fixed on site, cutting time and cost and removing the need for mechanical lifting.
A total of 300-plus Nexus XI soffit units were installed throughout the project, with the majority used on the Hillside towers to provide hanging soffits to the larger openings and lintels to the cycle store areas. Nexus XI Lintels were also installed on the lower rise Milton Avenue town houses in a combination of stretcher and soldier bond.
Nexus Next Generation Brick Faced Support Systems (PDF, 11.4 MB)
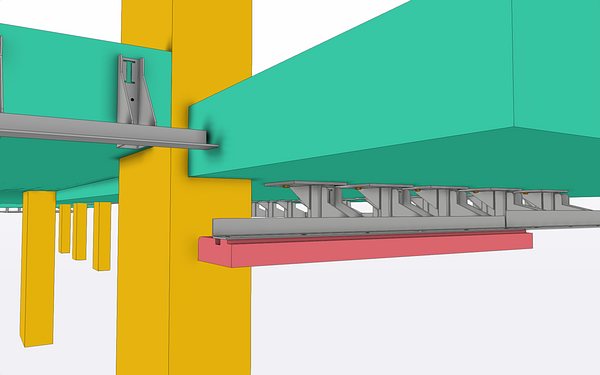.png, /rails/active_storage/representations/redirect/eyJfcmFpbHMiOnsibWVzc2FnZSI6IkJBaHBBc1dHIiwiZXhwIjpudWxsLCJwdXIiOiJibG9iX2lkIn19--57b112242737bb2a4956731b9452130c299156f4/eyJfcmFpbHMiOnsibWVzc2FnZSI6IkJBaDdDRG9MWm05eWJXRjBTU0lJY0c1bkJqb0dSVlE2RkhKbGMybDZaVjkwYjE5c2FXMXBkRnNIYVFLRUF6QTZDbk5oZG1WeWV3WTZESEYxWVd4cGRIbHBXZz09IiwiZXhwIjpudWxsLCJwdXIiOiJ2YXJpYXRpb24ifX0=--b2befa2e4f943dd704c0996d95d9f2d6abfe8b75/MicrosoftTeams-image%20(30).png 2x)
Leviat Project Manager, Chris Martin, said,
The ease of adjustment on the Nexus XI system enabled the contractors to easily achieve perfect alignment with the main façade brickwork and, as all of the brick slips were supplied from the same brick batch as the main building, colour matching was perfect throughout the project.” |
---|
Latest News
Leviat Launches New 300mm Type 4 Wall Tie for Wider Cavities
Leading construction accessories manufacturer, Leviat, announces the release of its new Ancon Staifix HRT4 300mm Wall Tie designed for use in wider walls with cavities ranging from 151-175mm. The addition of this product to the existing range will help specifiers and builders to meet the latest Part L regulations and achieve the more stringent U-values and building fabric requirements in the upcoming Future Homes Standard.
Enhanced Ancon IHR Head Restraints Now Accommodate 100mm Gaps Due to Customer Demand
Due to customer demand and changes to fire regulations, Leviat have successfully re-engineered the Ancon IHR range of internal head restraints, now accommodating gaps at the wall head of up to 100mm, extending the previous maximum of 75mm.