Celebrating 100 Years of Stainless Steel
Here, Ancon explains what makes stainless steel different to other materials and why it is often preferred to carbon or galvanised steels in structural applications.
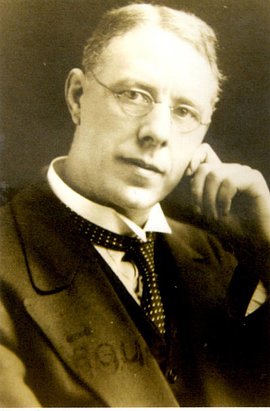
2013 marks 100 years since Harry Brearley, a Sheffield metallurgist working on a solution for high temperature erosion in gun barrels, discovered a super steel that was to have an enduring impact on everyday life.
In August 1913, when Brearley was experimenting with steel alloys containing high levels of chromium and low levels of carbon, he created what he called ‘Rustless Steel’. He noticed a sample with 12.8% chromium and 0.24% carbon did not show signs of rusting and showed unusual resistance to his corrosive etching agents. He had produced a martensitic stainless steel.
The term ‘Stainless Steel’ was first used by the cutlery industry to describe the non-corroding surface of the metal, even when in frequent contact with food acids, and it was quickly adopted as a generic name.
Today, the high strength, corrosion resistance, aesthetics and high/low temperature properties of stainless steel means it is not only standard in cutlery production but is widely used for washing machine drums, sinks, surgical blades, oxygen tanks, solar panels, tools, sculptures etc. The list is endless, with more applications being found all the time.
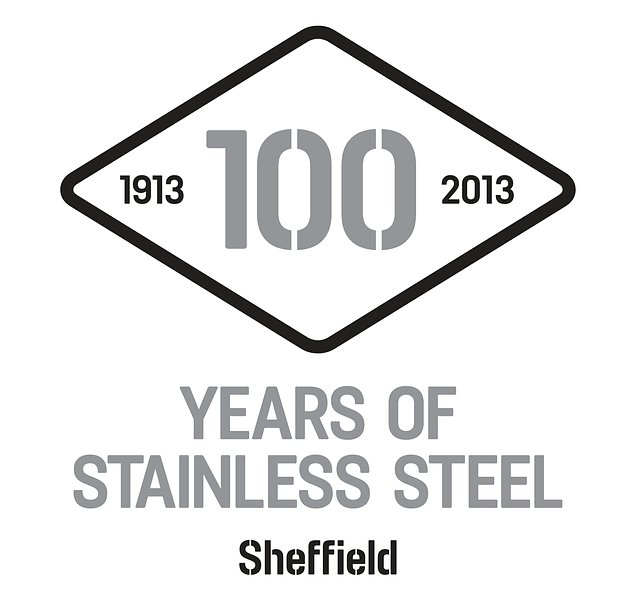
The use of stainless steel in the Construction Industry continues to increase as its benefits, especially those relating to sustainability, are more widely recognised. It comprises 65-90% recycled material content (limited only by the availability of scrap), offers low thermal conductivity and is 100% recyclable at the end of a long, often maintenance-free, service life.
Like Harry Brearley, Ancon is an integral part of Sheffield’s rich industrial heritage. The company has been fabricating steel in the city for over 130 years and was one of the first companies to recognise the potential for stainless steel in building applications, when it began developing its range of construction fixings in the 1960s.
Currently the Ancon product range includes stainless steel cavity wall ties, brick support systems, masonry reinforcement, shear load connectors and balcony connectors. All these products provide a critical connection within a building or structure, are invisible once installed and are permanently under load.
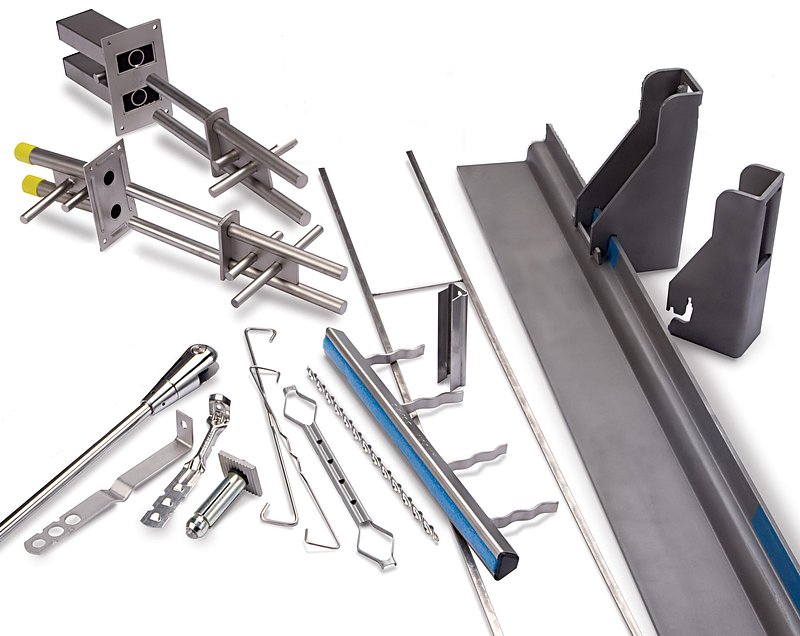
Inspection, maintenance or replacement of these fixings is either impossible due to inaccessibility or impractical due to the substantial costs and inconvenience it would involve. Therefore it is stainless steel that is preferred to carbon or galvanised steels in these structural applications as it provides the necessary integrity and assurance required by most asset owners.
A common misconception is that stainless steel is a single specific material. It is actually the name given to a group of corrosion resistant steel alloys which contain a minimum of 10.5% chromium.
The chromium reacts with oxygen in the air to produce a very thin, inert, chromium-rich oxide film on the surface of the steel and it is the presence of this passive film which provides the inherent corrosion resistant properties of the material. The layer is unlike an applied coating on plain carbon steel, such as paint or galvanising, in one very important way. If it is damaged by abrasion or mechanical means such as cutting, it re-forms immediately and continues to protect the steel.
Other elements can be added to the alloy to improve the material’s properties such as nickel and molybdenum.
Austenitic stainless steel is the most common family used for structural applications. It provides a good combination of corrosion resistance, forming and fabricating properties.
In 1924, Brearley’s successor at the Brown-Firth research laboratory in Sheffield, W H Hatfield patented ‘18/8’ stainless steel, known today as the austenitic grade 304 (1.4301) which is the most widely used grade worldwide. It typically contains alloying elements of at least 18% chromium and 8-10% nickel.
Most Ancon products are manufactured in grade 304 (1.4301), but for highly corrosive areas such as marine locations or heavily polluted industrial environments, Ancon recommends Grade 316 (1.4401). Here, the addition of a small proportion of molybdenum (around 2%) and an increase in the nickel content to 10-13% provide a more robust passive film and hence higher resistance to corrosion. In addition, the company continues to investigate new lean duplex grades and also provides products in grade 1.4462 duplex stainless steel - a high strength duplex stainless steel with a minimum chromium content of 22%, a nickel content of 4.5-6.5% and a molybdenum content of 2.5-3.5% which offers superior corrosion resistance especially against pitting and crevice corrosion.
Over its 130 year history, Ancon has firmly established a reputation for quality and innovation. Whilst we continually consider new materials for structural applications - such as our basalt-fibre wall ties and thermoset plastic thermal breaks - stainless steel still provides the platform for many of our latest new products.
In 2012, Ancon was awarded a prestigious Queen’s Award for Innovation for a stainless steel Lockable Dowel.
Ancon is a member of the British Stainless Steel Association.
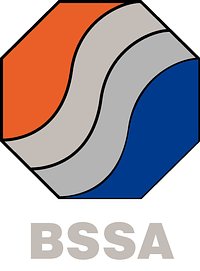
Latest News
Leviat Brings Innovation and Support to Super Trowel 2025
Engineered connection specialist Leviat is thrilled to return and support Super Trowel 2025, the UK’s leading exhibition and bricklaying competition for masonry professionals.
Entire Ancon Bolted Couplers Range now CARES Approved
Leviat is proud to announce that the entire range of Ancon bolted couplers has now achieved full CARES approval, highlighting our ongoing commitment to supporting construction professionals in meeting the highest standards of compliance, safety, and performance across the industry.