Agar Grove Estate, Camden
Key Project Facts
|
---|
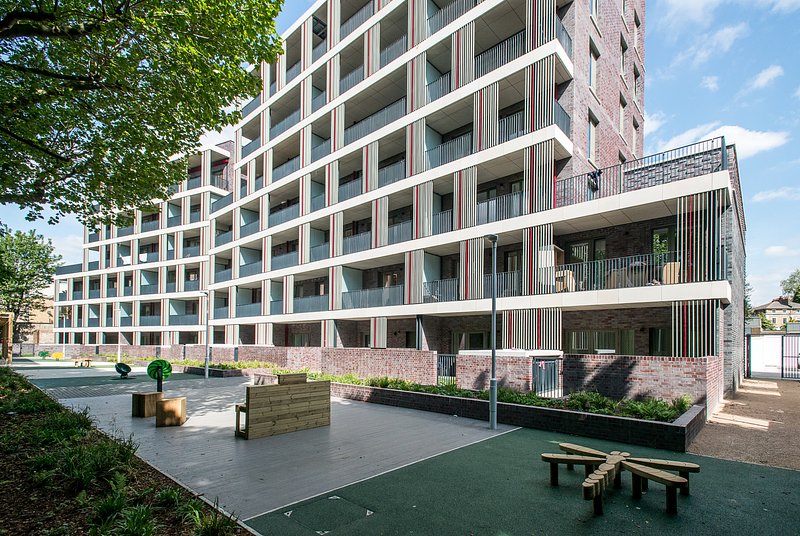
©David Hodgkinson Photography
The largest Passivhaus development to date in the UK, this 2.75 Hectare estate, originally built in 1966, is being regenerated including new buildings and refurbishment of the existing building to provide a mix of 500 one to four bedroom affordable homes.
Constructed across a number of 4-18 storey high rise blocks with ground-floor level retail units, this £118-million development has been undertaken by Camden Council in association with Camden’s Community Investment (CIP) Programme. It is the council’s largest CIP development to date, and one of the first estates of its type to feature a communal heating system.
The Challenge
The Passivhaus standard is recognised worldwide as the ‘gold standard’ in low energy construction. It is based on a ‘fabric-first’ approach, which requires high standards of insulation and airtightness from the external shell. To meet the demanding standard, the architects incorporated wide external masonry cavity walls, fully-filled with insulation and finished to extremely high standards of workmanship e.g. use of specialist airtightness tape at insulation joints.
Wall ties are an important structural component in cavity walls, ensuring the two leaves act as a homogeneous unit, but they create a repetitive thermal bridge through the insulation. The challenge was to find a wall tie solution that minimised heat loss across the insulated cavity.
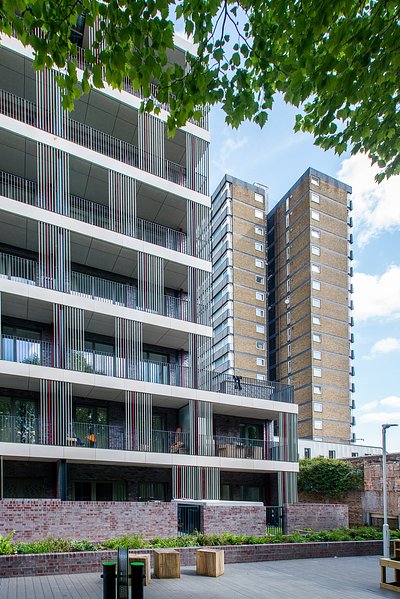
©David Hodgkinson Photography
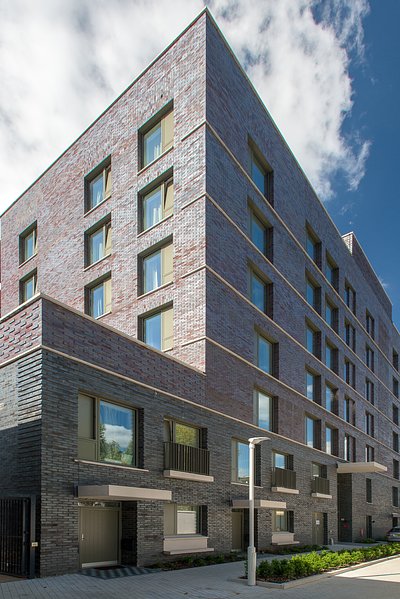
The Solution
The solution was to use Ancon Teplo wall ties. These unique ties, which comprise a pultruded basalt fibre body set in a resin matrix, have an extremely low thermal conductivity of just 0.7W/mK, twenty times lower than stainless steel wall ties.
Successfully used in many ultra-low energy and smaller Passivhaus developments across the UK, these innovative wall ties virtually eliminate heat loss across insulated cavities; their thermal conductivity is so low that they are disregarded in U-value calculations, performed either in the PHPP or to BS EN ISO 6946.
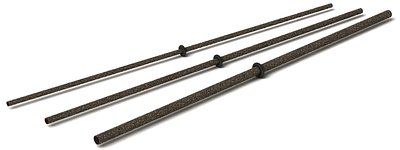
In the first phase of this project the original TeploTie with plain ends were used. One end was resin-fixed into the existing inner leaf of aerated concrete blocks using a special chemical anchor resin supplied by Ancon, with the other end built into the bed joints of the new outer leaf as work progressed. The range of different tie lengths meant that insulated cavities of up to 450mm could be accommodated.
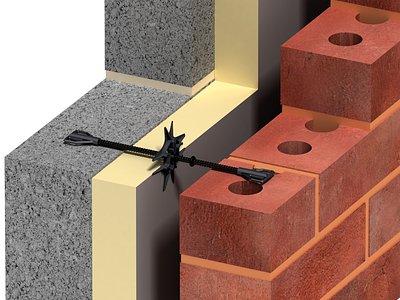
The second phase of this development, which involves the construction of four new-build blocks, is currently underway. It will feature Teplo-BF wall ties, specially designed to accommodate highly insulated cavities of up to 450mm in external walls of more traditional brick/block construction.
Teplo-BF new-build wall ties feature specially moulded safety ends that improve buildability. The user-friendly design offers exceptional mortar grabbing capability, making them particularly suitable for use with lime and other slow-drying mortars.
As well as the strength and versatility of Teplo wall ties, their ultra-low thermal conductivity means external wall widths can be optimised throughout the development, reducing insulation costs and maximising room space for tenants.
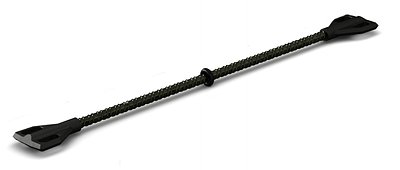
|
---|
Latest News
Leviat Brings Innovation and Support to Super Trowel 2025
Engineered connection specialist Leviat is thrilled to return and support Super Trowel 2025, the UK’s leading exhibition and bricklaying competition for masonry professionals.
Entire Ancon Bolted Couplers Range now CARES Approved
Leviat is proud to announce that the entire range of Ancon bolted couplers has now achieved full CARES approval, highlighting our ongoing commitment to supporting construction professionals in meeting the highest standards of compliance, safety, and performance across the industry.