The Goodsyard, Hockley Mills, Birmingham UK
Located on a former industrial site bordering Birmingham’s Jewellery Quarter Conservation Area, this unique mixed-use development delivers 390 one, two and three-bedroom apartments, commercial offices, retail outlets and a new railway ticket office, in addition to much needed new facilities for the city’s world-famous jewellery sector.
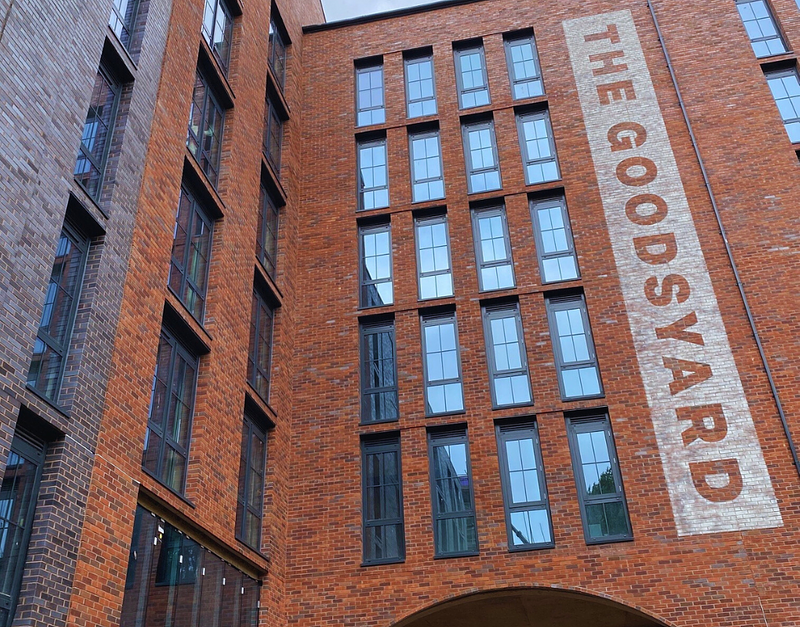
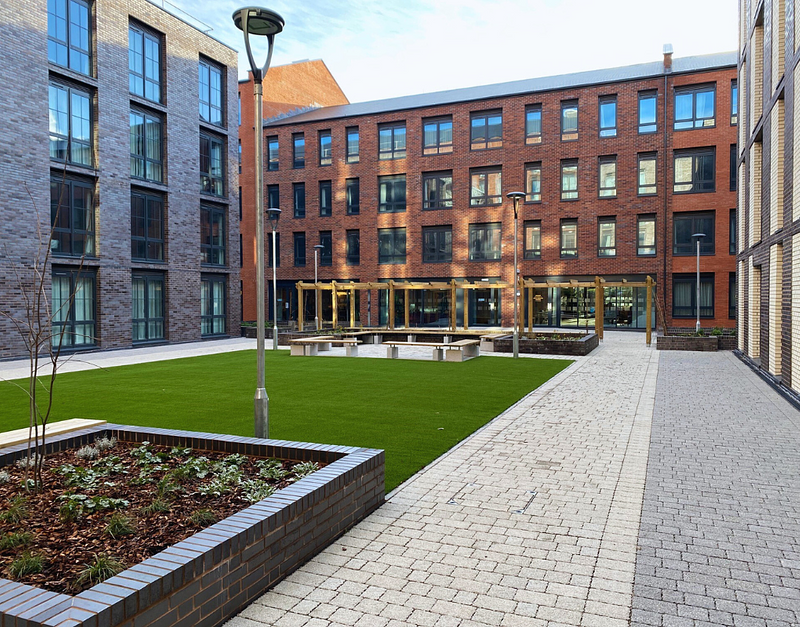
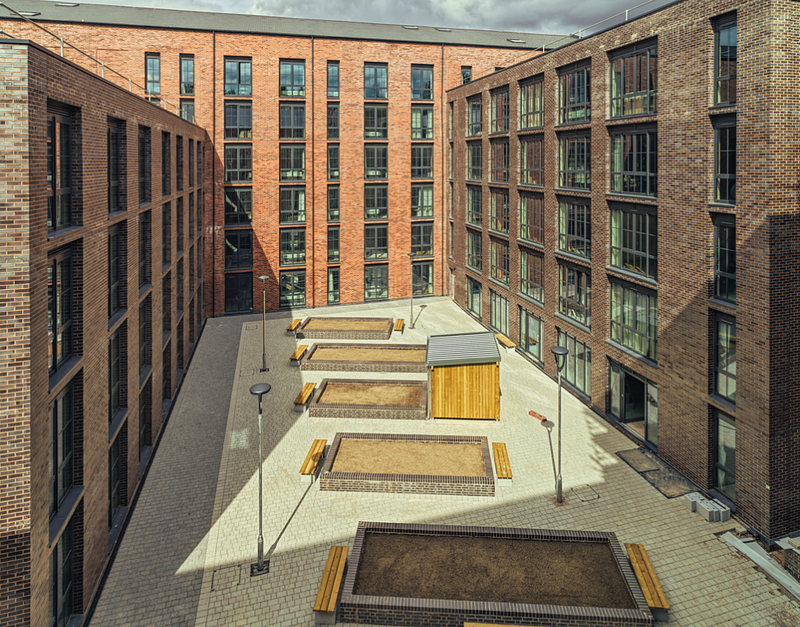

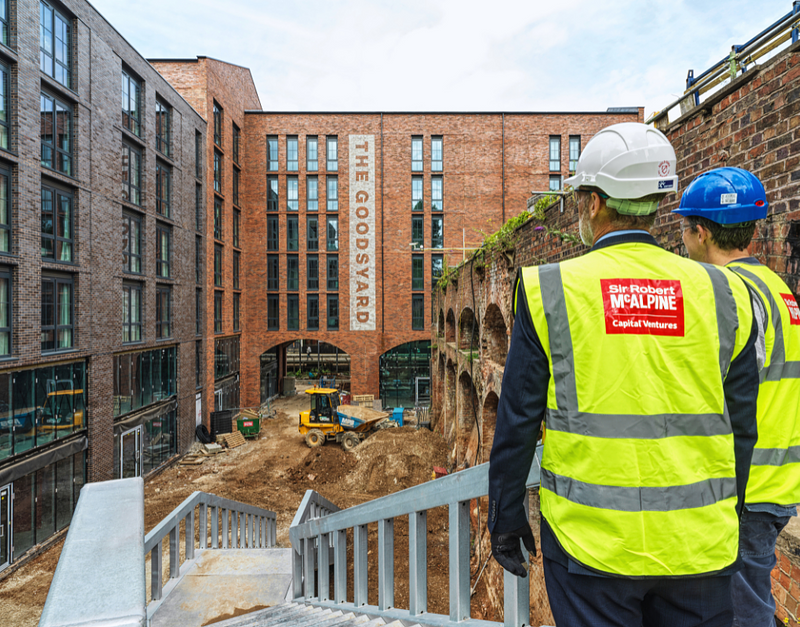
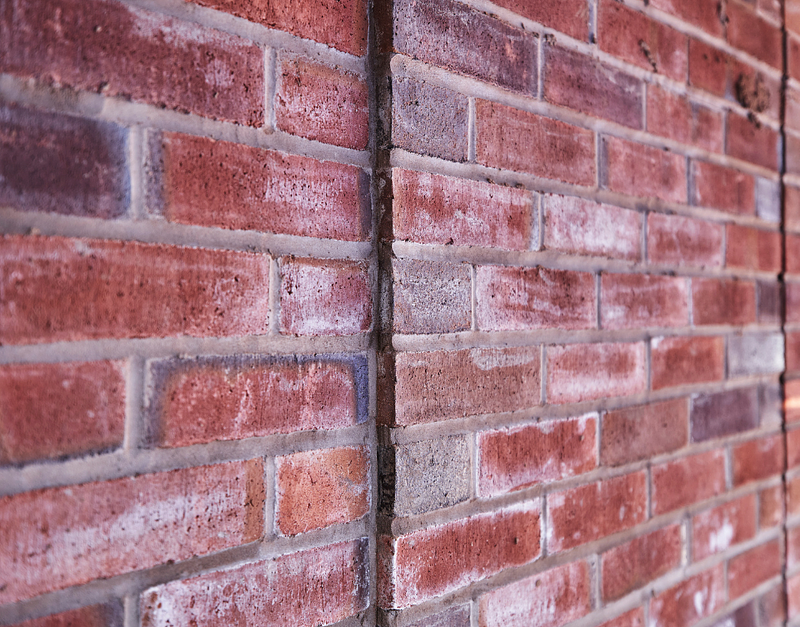
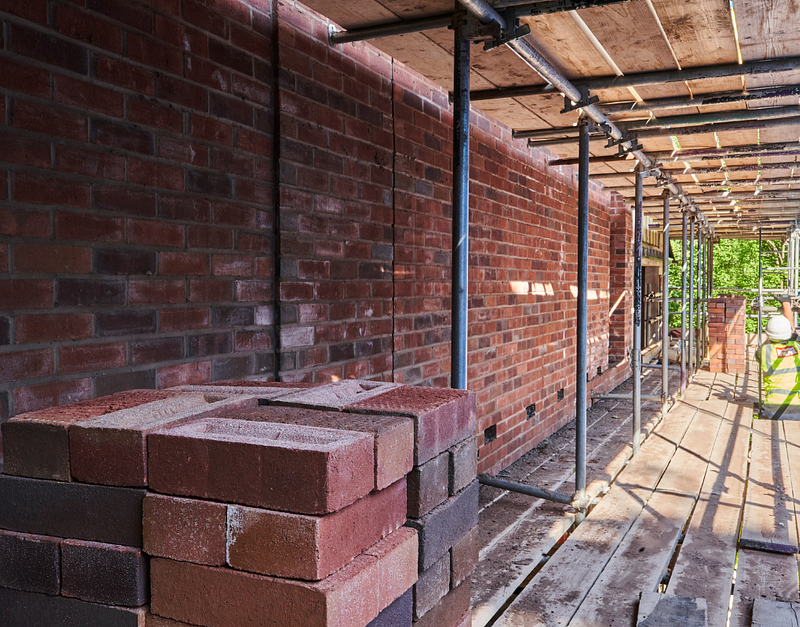
Sandwiched between busy railway lines and a public highway, and bounded by two historic cemeteries, the seven-building development varies in height between 3 and 7-storeys. It has been sympathetically designed to reference the area’s industrial heritage, with imposing brick facades, deep-set windows and distinctive archway detailing recreating the aesthetic of the historic warehouses that once defined the site.
The challenge
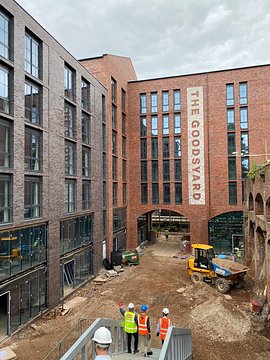
With buildings located close to the site boundaries, access for constructing the complex brickwork facades was limited, and was further complicated by the presence of old railway arches below the walkway immediately adjacent to the buildings. To overcome this, the external walls were to be constructed from the second floor upwards, using scaffolding. This was then be removed to allow access to the lower levels, which were constructed from the inside of the building, using an overhand technique.
The use of a site-cast concrete frame, with some slab depths down to just 225mm; post-tensioned slabs in some areas; recessed façade panels causing variations in cavity width and unusual corner detailing on the original drawings, placed extra importance on the choice and specification of the support system, that would carry the considerable weight of the external brickwork from slab edge fixings at every level.
Main Contractor, Sir Robert McAlpine, wanted to identify any potential issues that might delay progress, particularly in view of the size and unusually high-profile nature of the project, and was therefore keen to finalise the choice and full specification of the external brickwork support system at the earliest possible stage.
The solution
Having worked with Sir Robert McAlpine on similar projects in the past, Leviat was invited to submit proposals for brickwork support at the pre-order stage of the project. Working closely with brickwork contractor, Caxton, and McAlpine design engineers, the Leviat technical team carried out a detailed review of the project. Because of the early involvement, they were able to draw up a complete detailed and costed proposal based on the Ancon MDC stainless steel brickwork support system. This not only addressed all the physical limitations of the construction, but influenced key areas of the scheme design, including corner detailing, EPDM slab edge sealing and strand location in the post-tensioned slabs, simplifying installation and preventing potential problems once the project got to site. The team also presented proposals for a Project Tracker scheme listing any changes and additional costs to their package as the contract progressed, enabling McAlpine to better understand and manage project costs.
As a result, Leviat was invited to supply a complete package of masonry support and restraint fixings for this project. This included around 3,500 linear metres of Ancon MDC brickwork support, as well as Ancon Windposts to provide lateral support for the brickwork panels between floors. Ancon 25/14 Channel Tie Restraint systems and Ancon SD25 Wall Ties were also used throughout the project to tie-in the outer brickwork. Leviat provided technical support on and off-site and a single point of contact was assigned to speed up and simplify response to any project-related queries.
For more information contact our team on 0114 275 5224 or email masonry.uk@leviat.com.
Find out more
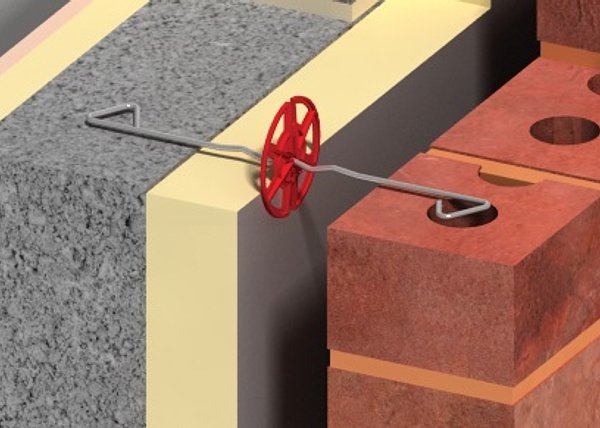
Wall Ties & Restraint Fixings
Wall ties and restraint fixings are an essential element in the stability of masonry panels.
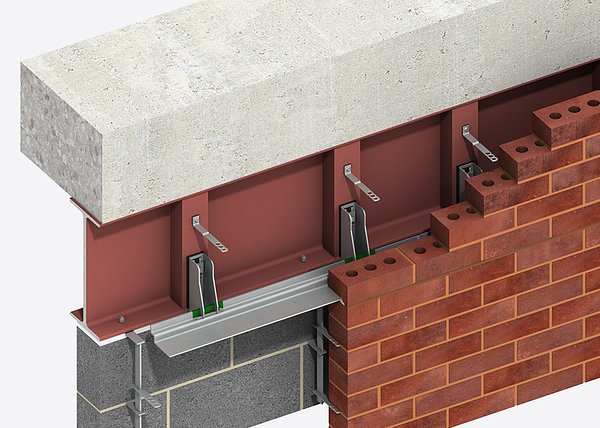
Masonry Support
Brick, block or stone cladding on steel or concrete framed structures is normally supported by stainless steel masonry support systems.
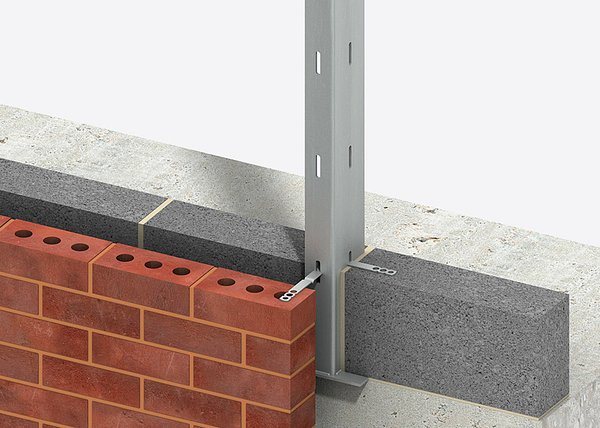
Windposts
Ancon Windposts are designed to span vertically between floors to provide lateral support for panels of brickwork.