Engineering Innovation in The Wave
This purpose-built hub is equipped with modern teaching facilities and is the university’s first net-zero in operation building. Designed to operate with net-zero emissions, the FOSS building features ground-source heat pumps for both winter heating and summer cooling, while solar panels generate electricity, further reducing its environmental footprint.
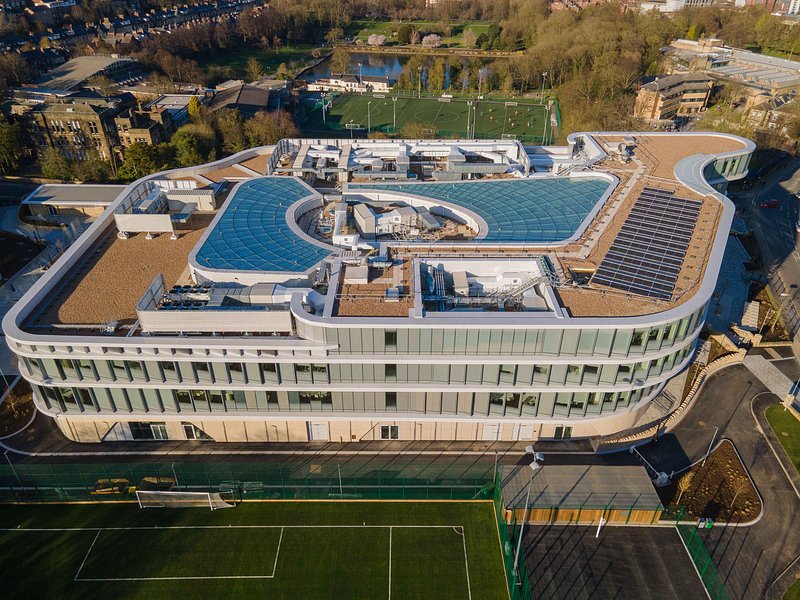
The construction journey began with a focus on addressing the unique challenges presented by the building’s design and tight timeline. As the project unfolded, it became clear that traditional labour-intensive methods would need to be enhanced with concrete solutions to ensure efficiency without compromising on quality. Leviat’s involvement was integral to achieving this, offering faster and more flexible construction techniques that allowed for smoother co-ordination across all teams, and quicker access for follow-on trades.
Collaboration was a key element throughout the project, particularly between Leviat, the specialist concrete frame contractor and the specialist post-tensioning contractor. By working together, they were able to provide both standard and bespoke concrete solutions, ensuring that the ambitious design could be executed within the strict deadlines. The close co-ordination between these teams streamlined the construction process, creating a cohesive system that met both structural and aesthetic goals.
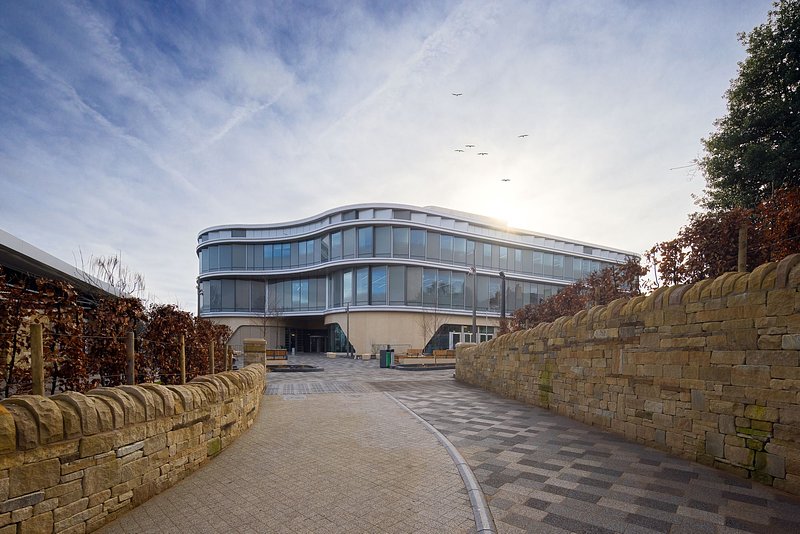.jpg, /rails/active_storage/representations/redirect/eyJfcmFpbHMiOnsibWVzc2FnZSI6IkJBaHBBblczIiwiZXhwIjpudWxsLCJwdXIiOiJibG9iX2lkIn19--c68e165c0434846a33ccc48ca8f6dec51cdc4a0d/eyJfcmFpbHMiOnsibWVzc2FnZSI6IkJBaDdDRG9MWm05eWJXRjBTU0lJYW5CbkJqb0dSVlE2RkhKbGMybDZaVjkwYjE5c2FXMXBkRnNIYVFLd0JEQTZDbk5oZG1WeWV3WTZESEYxWVd4cGRIbHBXZz09IiwiZXhwIjpudWxsLCJwdXIiOiJ2YXJpYXRpb24ifX0=--c8e8202432a5cd6f57887072b9ccdef60395b161/FoSS%20University%20of%20Sheffield_0351-Web%20(1).jpg 2x)
Continuity solutions
One of the solutions was Ancon Eazistrip, a system used to connect the core walls to the concrete slabs. This system offers a faster, safer alternative to traditional reinforcement bar methods, simplifying the connection process and allowing for quicker installation. Available in both standard and bespoke forms, it helps to ensure reinforcement continuity across construction joints, particularly in wall–slab and slab–slab connections.
This reinforcement continuity system can be custom designed to suit complex structural layouts, which was particularly beneficial for the Wave building’s intricate design. Not only did this save time, but also it improved site safety by eliminating protruding bars that can pose a risk to operatives, while also avoiding damage to formwork caused by drilling to accommodate protruding bars.
Another critical innovation was the use of lockable dowels at movement joints in the post-tensioned slab. Traditionally, movement is often accommodated by leaving ‘pour strips’ – 1m-wide openings in the slabs, which are filled once the concrete has cured to provide the desired continuity in the frame. By incorporating Leviat’s Ancon Lockable Dowels, the need for pour strips was removed, speeding up construction and preventing the usual 30-day delay associated with slab propping at each level. This allowed follow-on trades unhindered accesst o the slabs and contributed to a safer construction environment, as the absence of pour strips meant no exposed post-tensioning strand and fewer trip hazards for operatives on-site.
Punching shear
Ancon Shearfix, a system designed to address the effects of punching shear at column heads, was also a key component of the FOSS building’s structural design. Preventing punching shear due to slab weight can be a serious concern in large concrete structures. The traditional solution of using a complex configuration of shear links can be time-consuming and labour-intensive, requiring individual calculations to determine the shear forces involved – with every column being different. However, the Shearfix system offered a more efficient alternative. A software-designed system, it is preassembled into a stud-rail system that can be installed quickly, significantly reducing the time required to address punching shear and allowing for faster work on the slabs. This system eliminates the need for specialist steel fixers and speeds up the entire process, which was particularly important for keeping the project on schedule.
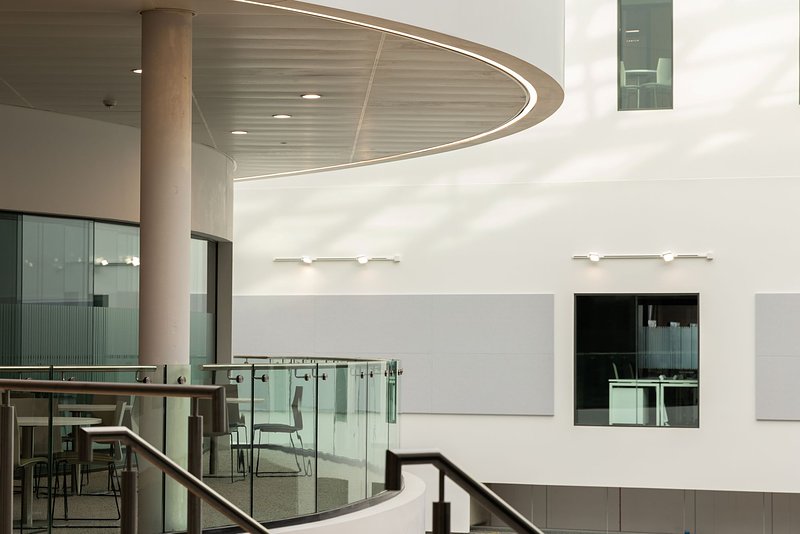
The FOSS building demonstrates how collaboration, innovative engineering and bespoke concrete solutions can help bring ambitious architectural designs to life. By embracing modern construction techniques and advanced concrete solutions, the project met its design, timeline and safety objectives, pushing the boundaries of what is possible in contemporary construction.
Latest News
Leviat Brings Innovation and Support to Super Trowel 2025
Engineered connection specialist Leviat is thrilled to return and support Super Trowel 2025, the UK’s leading exhibition and bricklaying competition for masonry professionals.
Entire Ancon Bolted Couplers Range now CARES Approved
Leviat is proud to announce that the entire range of Ancon bolted couplers has now achieved full CARES approval, highlighting our ongoing commitment to supporting construction professionals in meeting the highest standards of compliance, safety, and performance across the industry.
0 comments
Please leave a comment using the form below