Thermal efficiency in buildings - can we afford to turn a blind eye?
Jeff Edwards, Senior Engineer, Masonry at Leviat
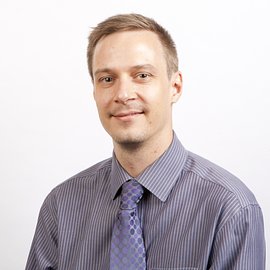
It is widely accepted that designed thermal performance is rarely achieved under actual site conditions, and this 'performance gap' becomes more significant as thermal standards increase. So, are we right to continue sweeping the problem under the carpet? Is the problem just down to inconsistent installation, or do manufacturers carry some of the responsibility?
Leviat has been at the forefront of development of products which help reduce or eliminate cold-bridging – from low thermal conductivity wall ties to insulated balcony connectors – all aimed at maintaining the thermal integrity of the building envelope, helping to create better buildings for the future. Wishing to build on this expertise, as part of both undergraduate and postgraduate research supported by Leviat, I decided to focus on the thermal performance of our masonry product range with a view to driving improvement and innovation within the range.
Addressing the problem
Examining previous data on the as-built performance of external wall constructions it was clear that the discrepancy between designed and actual site performance was most prevalent in masonry cavity walls, with partial-fill walls demonstrating the greatest variance. This initially supported the theory that inconsistent installation could at least partly explain the problem: installing partial-fill insulation requires a greater degree of on-site care, both to ensure it is properly secured against the inner leaf, and to avoid gaps at interfaces and junctions.
However another related issue is also at play: how relevant are the thermal models created by designers, and how representative are they of the as-built condition? Clearly if on-site variation is greater in masonry cavity walls, it's expected that greater deviations from the designed thermal performance come as a result, particularly if detailing for the insulation is lacking or the importance of this is not properly communicated to the builder.
From here, my focus turned to products from the Ancon range which interact with the cavity insulation over larger lengths or areas, and I decided to investigate windposts.
Windposts are used largely in commercial and multi-storey residential developments to provide lateral support to long panels of brickwork without the need for piers of supporting walls, or to provide hidden support around large window or door openings. Current design trends mean their use is on the increase as building owners desire more open plan spaces, so this was an appropriate subject for investigation.
Being positioned within the cavity of a masonry cavity wall, windposts are a product that interact significantly with the surrounding insulation along the full height of the wall. In the case of angle sections, the windpost section also penetrates the blockwork of the inner leaf providing a direct path for thermal energy to be lost to the cavity. Thermal performance is not typically a consideration to the specifier, with sections being selected primarily on structural requirements resulting in a wide range of depths and thicknesses to deal with.
Windposts inevitably create discontinuities in the insulation layer, along with other small gaps and voids which can be tricky to deal with and easy to overlook during design and construction, therefore, they have the potential to increase localised heat loss through the wall. Additionally, a search of manufacturers’ literature contained very little information on either the thermal performance of the posts themselves, or how to effectively fit insulation in and around them to ensure continuity of thermal performance across the wall area. As a result, installation of insulation around windposts tends to be ad-hoc rather than being specifically detailed, and designers are stuck with either using a default thermal transmittance (ψ-value) provided by BRE in BR 443, or undertaking more complex analysis which may or may not be truly representative of how it is built on-site.
So, three questions were present. How applicable is the default value in BR 443 to the wide range of section sizes available? Could windposts be contributing to the performance gap? And if they do, how can we as a market leader address the issue?
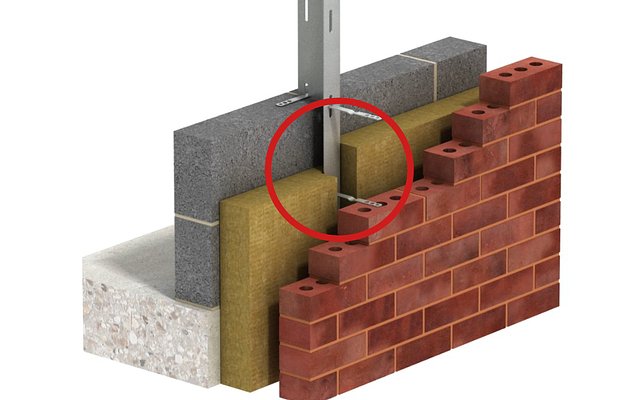
Increased thermal transmission through gaps and voids created by standard angle section windposts
Finding a solution
To investigate the problem I carried out a series of analyses of the popular Ancon WP2 range of angle-type posts looking at the thermal transmission through the span of the section. Taking the BRE ψ-value of 0.18W/mK from BR 443 as a limit, I carried out investigations using two different wall specifications; one designed to satisfy Building Regulations Part L1A, and one achieving the standards required by the Code For Sustainable Homes – Level 4.
Analyses were carried out in incremental stages, starting with insulation hard up to the side of the post. Small gaps were then introduced between the windpost and the adjacent insulation panels each side, increasing in 5mm increments up to 50mm, in order to gauge each section’s sensitivity to these gaps. Posts were analysed both with and without insulation behind the flange.
Whilst most of the WP2 windposts sat comfortably at or below the 0.18W/mK default value with insulation tight to the post side, it was found that some of the largest section sizes already slightly exceeded the default value in the “perfect build” scenario. Once gaps of 5-10mm were introduced, around half of the range exceeded the default value, and at 20mm all were above this figure, with the worst performer dropping to 0.28W/mK once the gap reached 50mm.
Furthermore, simply omitting the insulation behind the flange increased the sensitivity of the post to small gaps significantly meaning that, with only small 5mm gaps to the insulation, much of the WP2 range was above or close to 0.18W/mK. These results reflected the fact that where designers are using this value in their building model, it cannot always be guaranteed, especially when apparently minor variations from the “perfect build” scenario are considered.
Clearly, Windposts and other cavity intrusions have the potential to seriously downgrade the thermal performance of the wall unless correctly specified, detailed and installed. Getting this right is important if we are to achieve the sort of levels of fabric heat loss now being considered in our race for zero-carbon construction, particularly given the evidence that more stringent thermal specifications are harder to realise in practice.
But do manufacturers also have a role to play and are the windpost designs currently on the market fit for future demands? Masonry is a very popular type of construction in the UK, and the onus lies with manufacturers such as Leviat to provide products and solutions which ensure that masonry can continue to be a popular choice in the future. At Leviat, we always aim to be ahead of the pack, providing customers with the most advanced innovative solutions to help them meet the building challenges of tomorrow.
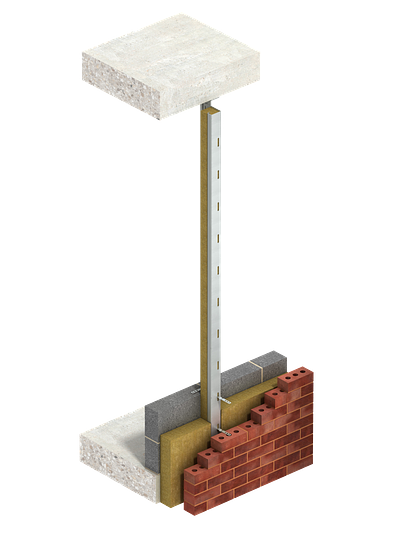
A revolutionary new product
So, along with our technical team and design specialists, I'm delighted to announce that the ground-breaking Ancon Thermal Windpost (TWP2) is now available. The Thermal Windpost has been a result of extensive research and testing, and I am extremely proud to have been part of the team creating a product that addresses one of the many thermal heat loss issues across a building’s fabric.
Offering up to an impressive 70% reduction in thermal transmission through the span of the windpost, the Ancon Thermal Windpost guarantees that the BRE level for thermal performance is met in all cases, an assurance otherwise unseen on the windpost market.
Our innovative new solution features integral non-combustible insulation to ensure continuity of insulation in the cavity, and therefore it sits level with the outside face of partial-fill insulation. With two perpendicular surfaces at the interface between the insulation and post, and consistency in post depth for a given insulation thickness, it is easy to butt the insulation hard up to the section consistently. For foil-backed insulation, panels can also be taped to the section to further enhance performance. For the installer, this provides the additional benefit of eliminating time-consuming cutting of insulation to fit behind/around the windpost, increasing the overall speed and consistency of installation.
The inclusion of a thermal slot array ensures that thermal energy has a longer more arduous path to the cavity, disrupting the direct path for the thermal energy. This means that when insulation is hard up to each side of the post, a ψ-value of between 0.04-0.06W/mK through the span of the section can be achieved (of course, further analysis of the floor-to-wall junction is required to account for the end connections).
By manufacturing the windpost from stainless steel with a teardrop fold for strength, and engineered to minimise weight, this light-gauge design is up to 35% lighter than traditional windposts, making it easier to handle and install onsite.
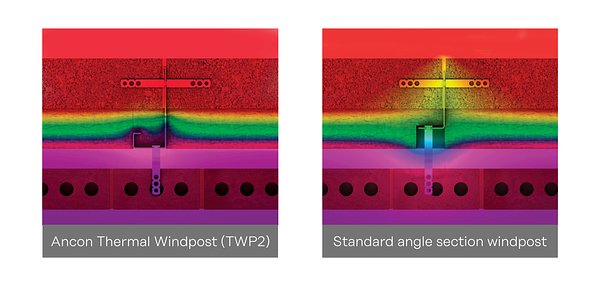
In short, the new Ancon Thermal Windpost (TWP2) is a game changer for the industry, which we firmly believe will help both contractors and building designers realise the thermal performance aspirations of the detail.
For more information on the Ancon Thermal Windpost (TWP2) click here, or contact us.
Latest News
Leviat Brings Innovation and Support to Super Trowel 2025
Engineered connection specialist Leviat is thrilled to return and support Super Trowel 2025, the UK’s leading exhibition and bricklaying competition for masonry professionals.
Entire Ancon Bolted Couplers Range now CARES Approved
Leviat is proud to announce that the entire range of Ancon bolted couplers has now achieved full CARES approval, highlighting our ongoing commitment to supporting construction professionals in meeting the highest standards of compliance, safety, and performance across the industry.
0 comments
Please leave a comment using the form below